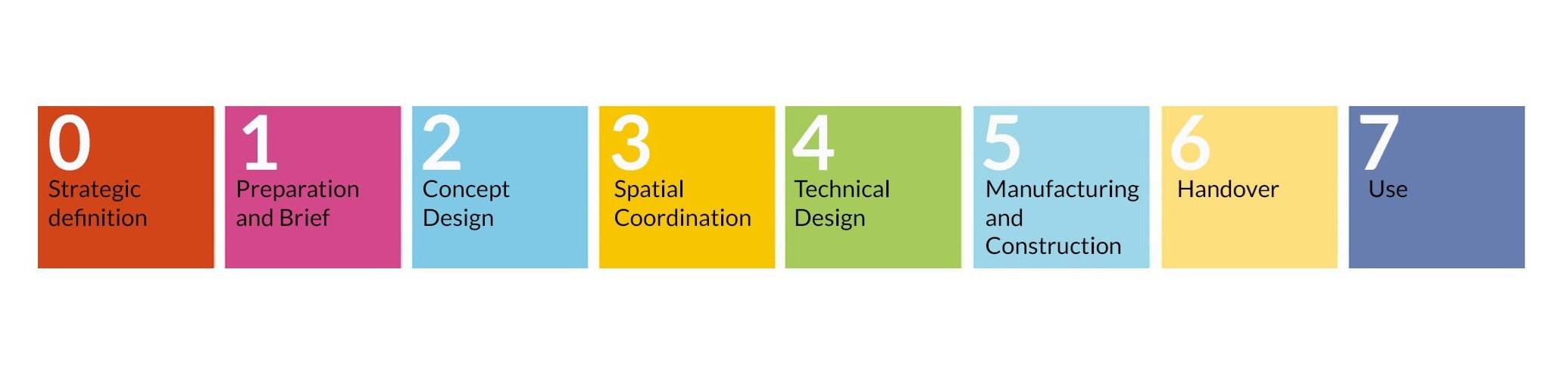
Passivhaus and the RIBA stages
Delta Q work on the design and delivery of Passivhaus buildings through every stage of development. Here are key considerations for successful delivery of Passivhaus standards at each of the RIBA Plan of Work Stages.
Stage 0
From the outset, it is useful to include strategic Passivhaus objectives in the project definition. Advising clients on the implications of Passivhaus, we also assist with the development of policy and practice supporting low energy building implementation across their organisations.
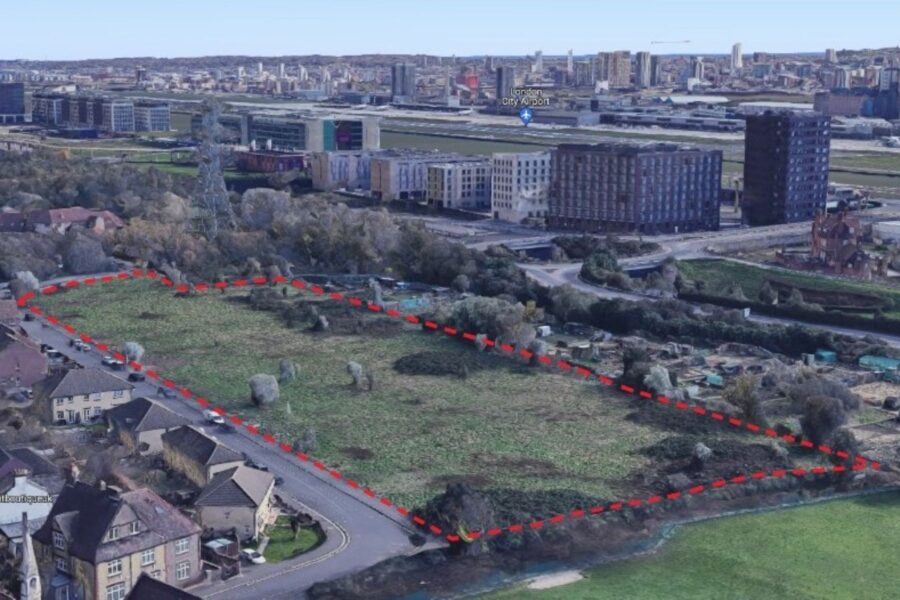
Stage 1
At this stage, clients and their advisers should become aware of the costs and constraints associated with Passivhaus and the implications for the design of the building and ensure that these are reflected in the project brief. Our strategic advice enables clients to properly consider the impact of adopting the Passivhaus Standard on a project-by-project basis. We develop generic and bespoke Employers’ Requirements for use across a range of projects.
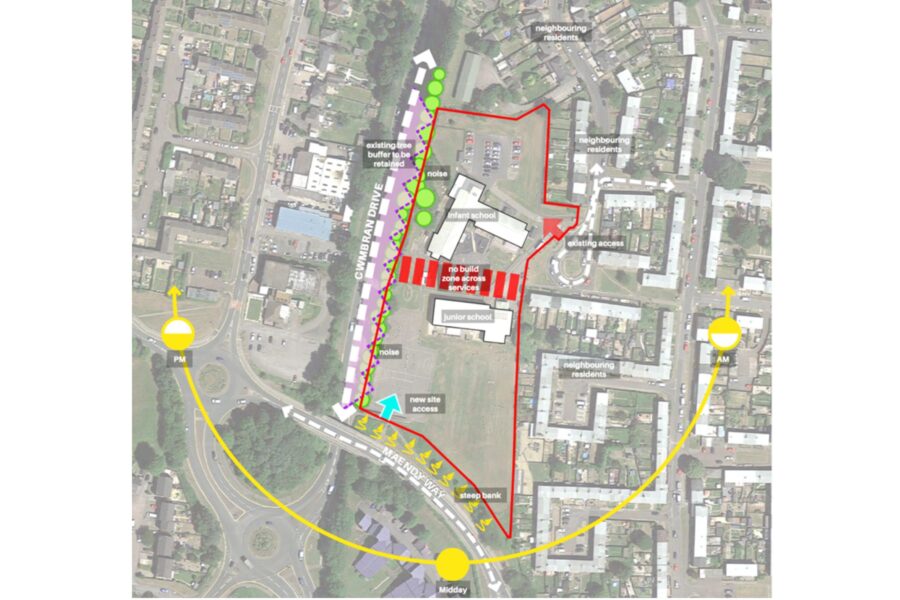
Stage 2
This is where our design input begins. The location, orientation and form of a building all have a significant impact on building energy outcomes and on the ease with which the Passivhaus Standard can be met. Considering project objectives and site constraints, we advise designers on how these early design decisions affect achieving the standard.
Feasibility studies to consider whether and how the constraints of Passivhaus and EnerPHit design can be aligned with project objectives and resources are also undertaken at this stage.
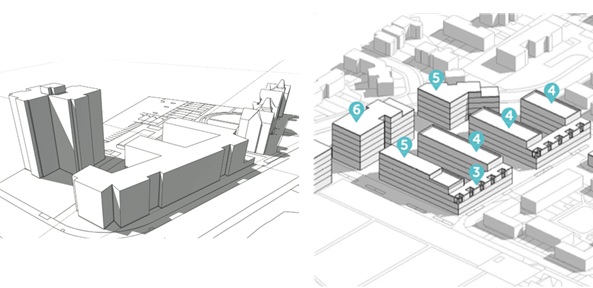
Stage 3
This stage includes window, shading and ventilation, design for daylighting, views and summer comfort, together with key aspects of the internal layout such as stair cores, access corridors, stacking and service risers and plant locations. Construction method may also be a factor in spatial co-ordination or conversely spatial co-ordination may dictate construction method. For apartment blocks, definition of the thermal envelope and consideration of the air test strategy is advised. At this stage we develop the first pass PHPP model to determine U-values and wall thicknesses and inform design decisions and test options.
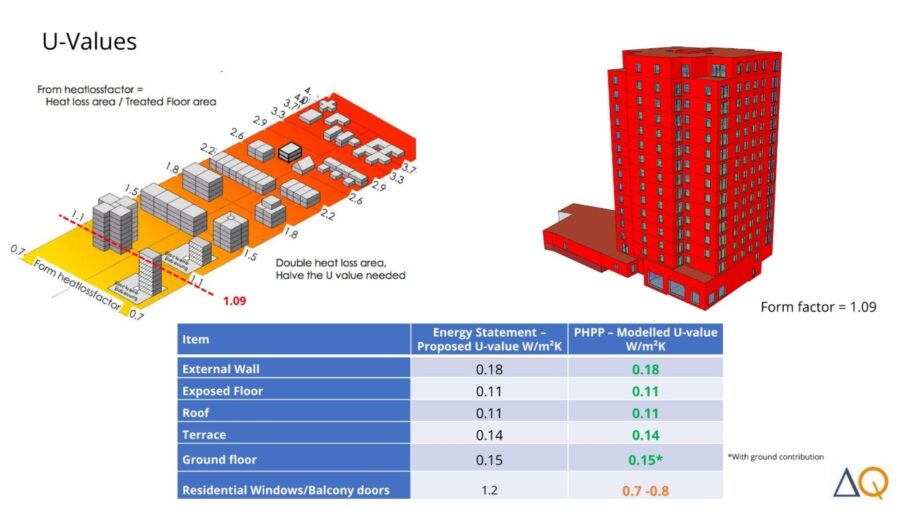
Stage 4
Development of detailed designs and quantification of the energy impacts run in parallel through this stage. While we use our experience to advise on tried and tested methods, we are also open to new approaches. Technical design typically includes the following:
- Structural and architectural co-ordination
- Junction detailing
- Airtightness and testing strategy
- Thermal bridge modelling
- Energy efficient and Passivhaus compliant building services design and specification
- Detailed energy assessment of plug in equipment
- PHPP modelling
- Evidence gathering
- Pre-construction certifier review
- Procurement advice
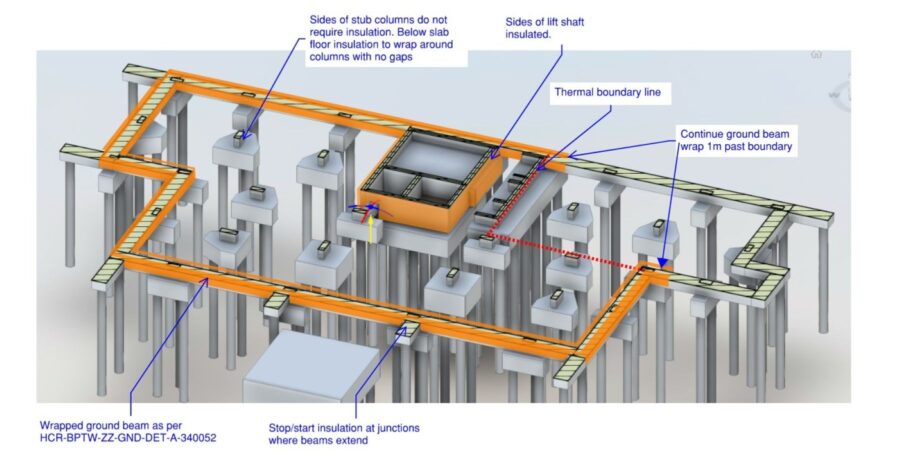
Stage 5
At the beginning of construction we prepare the contractor’s team for implementation through:
- Assistance with induction materials
- Design review with specialist sub-contractors
- Supplier demonstrations
- Benchmarking of initial installations to confirm the required quality
- Setting up evidence collection system
We then provide a supporting role throughout construction, enabling the Passivhaus Champion to demonstrate that construction is in line with the design. Our role includes:
- Continued monitoring of site quality
- Troubleshooting
- Certifier liaison
- Commissioning advice and support
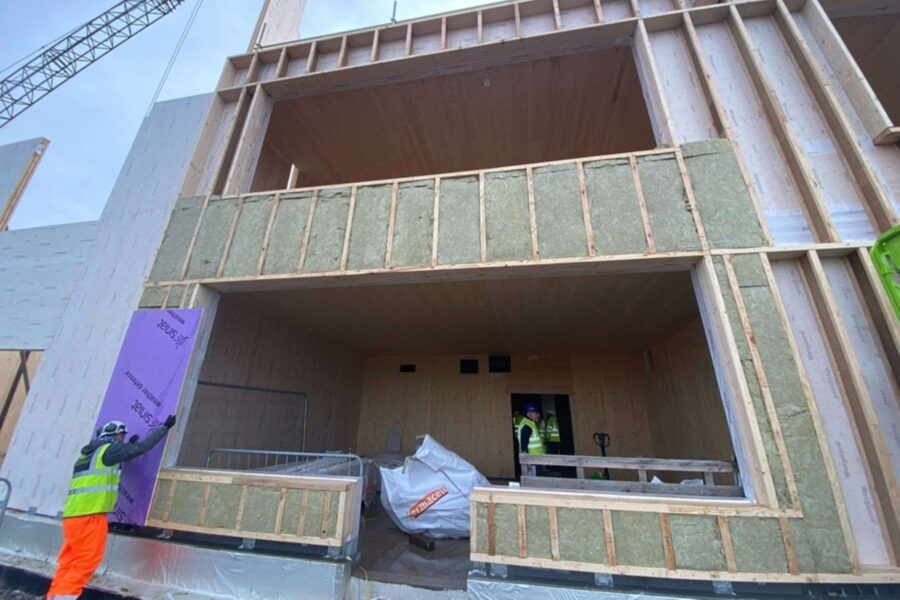
Stage 6-7
We aim to achieve Passivhaus certification within six weeks to three months of practical completion by managing the information flow throughout construction and keeping certifiers appraised of likely timing of their final certification review.
Beyond certification we are involved in snagging, handover and setting up monitoring. Building performance evaluation is an integral part of our service. This is usually a relatively light touch process involving setting up data collection, informal occupant interviews and reporting on performance against Passivhaus criteria and PHPP model results, but this can be adjusted to suit project needs.
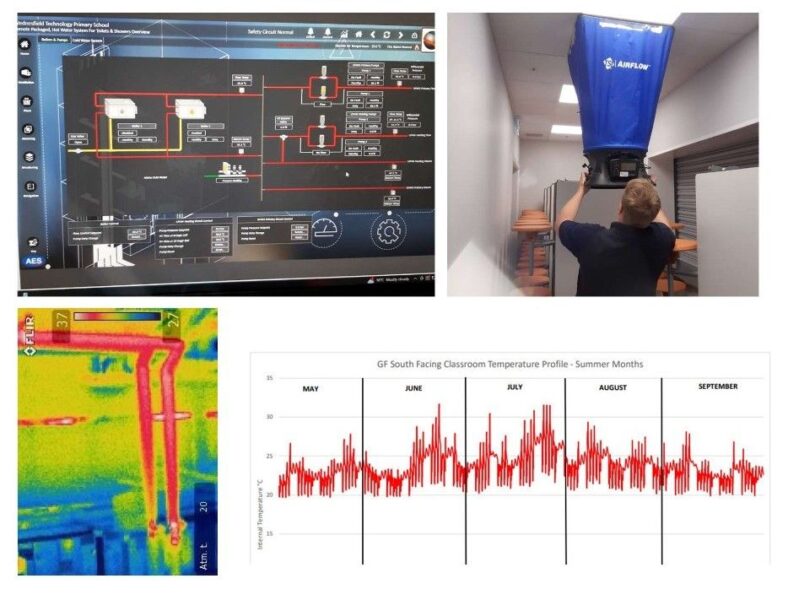