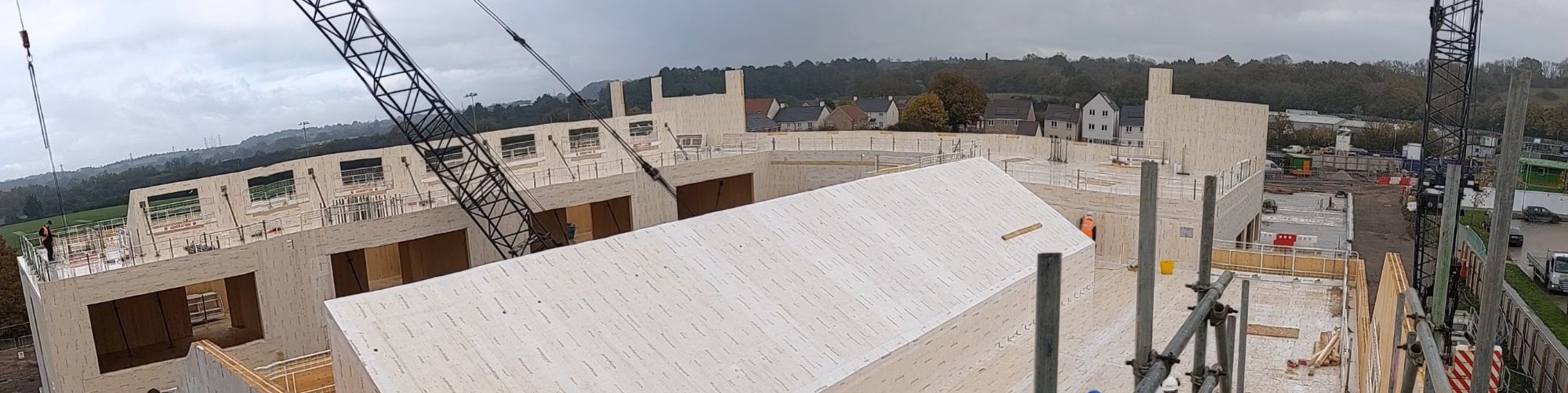
How to Make Passivhaus Easier: Three Key Rules
Delta Q are rarely approached these days about a new project without Passivhaus being mentioned. Most architects and many clients have an understanding that Passivhaus represents the highest standard of energy efficiency; some have an understanding of the energy performance gap and are aware that adopting the Passivhaus standard will help to eliminate it; others are aware that Passivhaus provides excellent thermal comfort and indoor air quality; but few make it easy for themselves as they set off on a journey towards creating what is still a very special type of building..
Of course, there are some who are sceptical, with concerns about cost, a preference for ‘natural’ rather than mechanical ventilation, or perhaps a leaning towards generating low-carbon energy rather than focusing on demand reduction. This article is not intended to persuade people that Passivhaus is the correct or best way to build, but rather to lead people in the right direction when they embark on a Passivhaus project by providing three simple rules to follow from the outset. Following these rules allows the designer to get the basics right, so that achieving Passivhaus or near-Passivhaus performance, with the right team, can be easy. (Of course, the normal difficulties of planning, procurement, funding, etc. will still apply.)
Below are some images from designs where we were asked to advise on Passivhaus. Whilst the designs are crisp and modern, they all exhibit some of the challenges that the rules below will help to overcome.
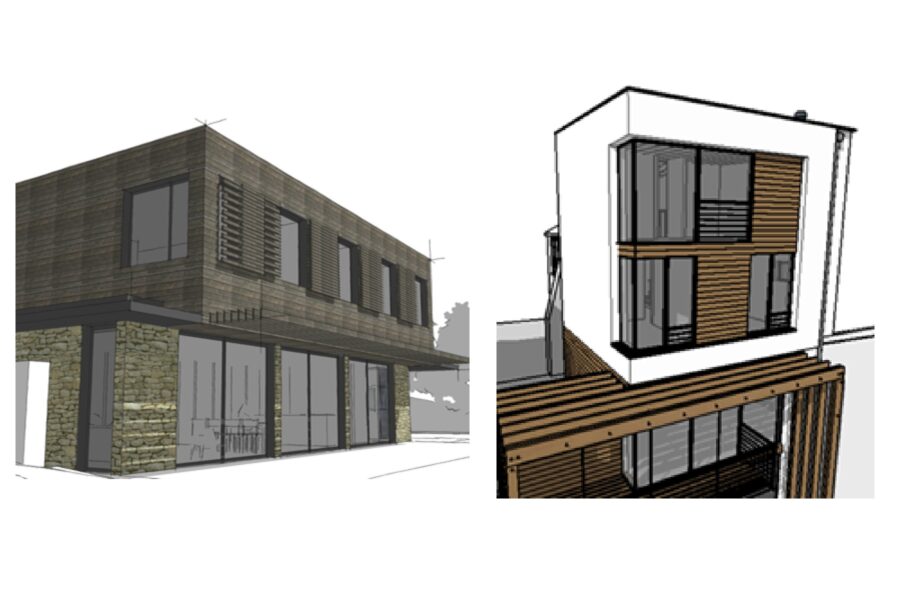
Rule 1: Adopt a simple form
All too often when we are approached about a new project, the form of the building has already been fixed, either in the mind of the client or architect, by some initial drawings or by planning consent. This creates special challenges for low-energy buildings.
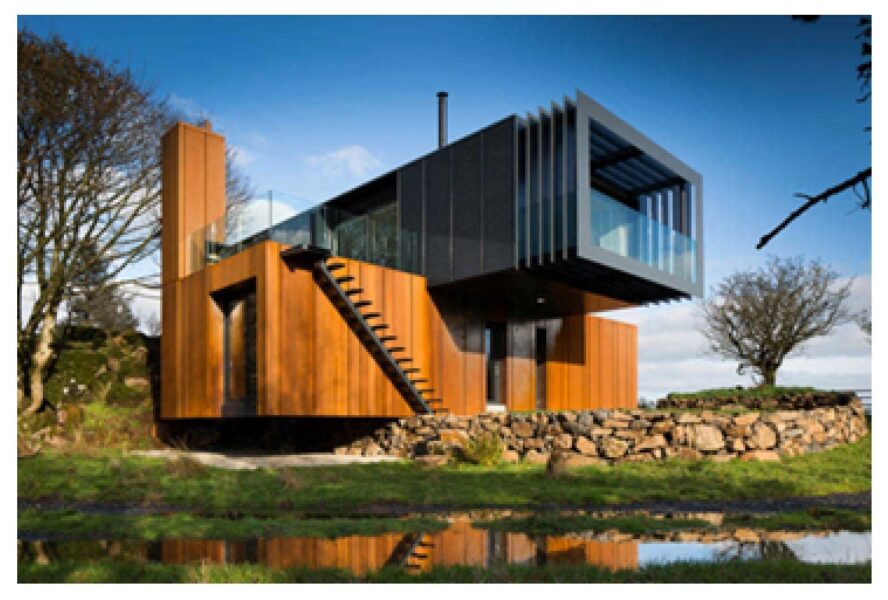
The building above involves cantilevers which require complex structures. Corner windows are a particular problem because they need structure to hold the weight above the corner. The effect of these complexities is to increase the surface area for heat loss, whilst at the same time creating junctions where it is difficult to achieve continuity of insulation and airtightness. These complex forms and structures are more expensive to build, and Passivhaus exaggerates the extra expense.
At the design stage, complex junctions lead to additional design and analysis work, such as thermal bridge modelling and selection of expensive materials such as Foamglas and aerogels. Complex designs can lead these costs to spiral out of control, at which point the usual response is to compromise on energy performance because the form is locked in by planning.
The image below left shows the output of a thermal bridge model for a junction which calculates the linear heat loss coefficient (ψ value) through the junction. The junction illustrated is a masonry cavity wall supported on steel at an exposed soffit. The junction used Foamglas blocks (shown right) to limit heat loss from the inner skin of the cavity wall to the steel.
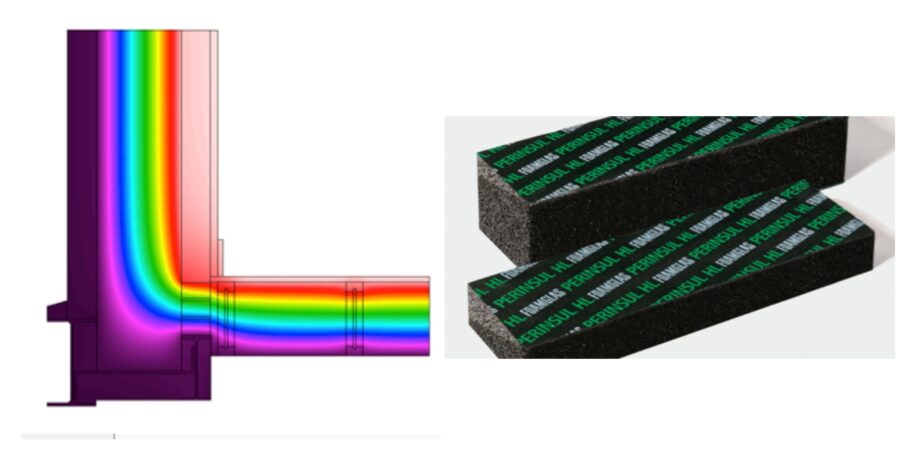
Planning the airtightness strategy through complex junctions can be an involved process, which it is virtually impossible to address once on site. The image below left was used in planning the air barrier for a steel-to-steel junction on a Passivhaus project. It would be better if the junction were designed out, but with care, airtightness through the barrier junction is possible. The photograph, below right, shows a junction between three steel beams (alignment marked in red) and the attempt to make it airtight. The contractor had to resort to expanding foam between the steels to do the best they could, but this is far from ideal.
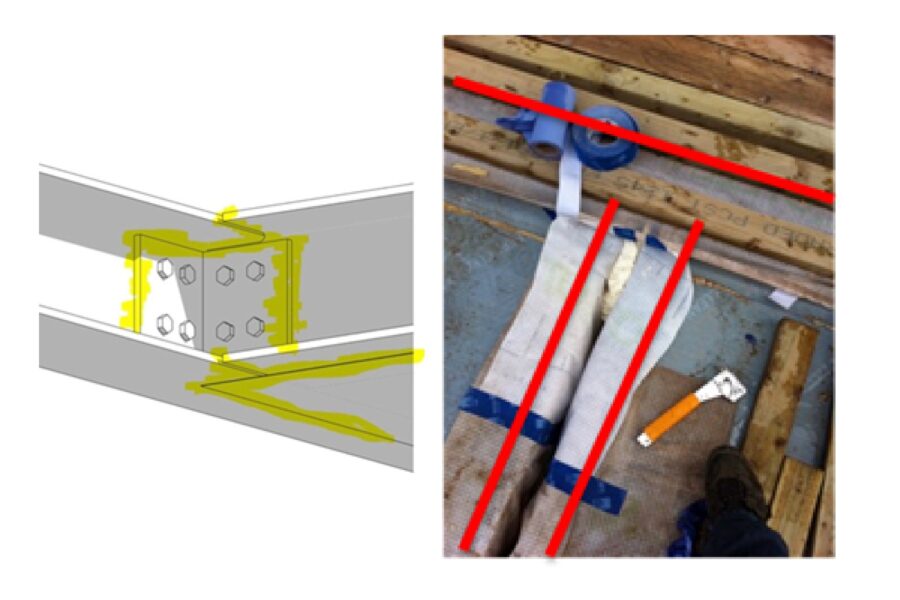
In summary: keep the form simple; where possible align each floor directly on top of the one below; avoid the stack of boxes approach; and in doing so, save money and make low-energy design easy.
Rule 2: Windows – not too big, not too small – just right
Passivhaus requires triple-glazed windows in temperate and cold climates to ensure optimum thermal comfort and avoid surface condensation, but there is much more to it than this. Getting the fenestration design right is critical to the successful performance of low-energy buildings and a requirement for Passivhaus.
Too much glazing results in excessive solar gain and overheating; small windows reduce beneficial glass area at the expense of the frame; permanently shaded windows lose heat which cannot be offset by beneficial solar gain; and window installation needs to be properly designed and implemented to minimize thermal bridging and achieve the required airtight construction. The design is a fine balance between these sometimes competing factors.
Whilst every building has its own particular setting and circumstances, a good starting point for total glazing area is 20% of floor area in proportions: 50% south: 20% east: 20% west: 10% north. Increasing the total area of south, east, and west-facing windows means shading is required to avoid overheating, and at about 30% of the floor area, moveable shading is required. Large areas of west-facing glazing are particularly problematic. The requirement for shading can often result in knock-on effects such as thermal bridging by shading supports.
Small windows, including those created by dividing a larger window with mullions and transoms, and elongate windows, increase frame area at the expense of glass. Typically with triple glazing, the glass U-value is lower than the frame U-value, with the heat loss through the window being in the region of five to six times that through the adjacent wall. While heat loss through glass is offset by solar gains, that through the frame is not. For these reasons, small frame areas and large glass areas are favoured.
Whilst shading can be beneficial to limit unwanted solar gains, heavily shaded windows lose much more heat than the neighbouring walls while providing only limited beneficial solar gain. Permanent shading by fixed louvres, for example, or by parts of the building structure should be minimised.
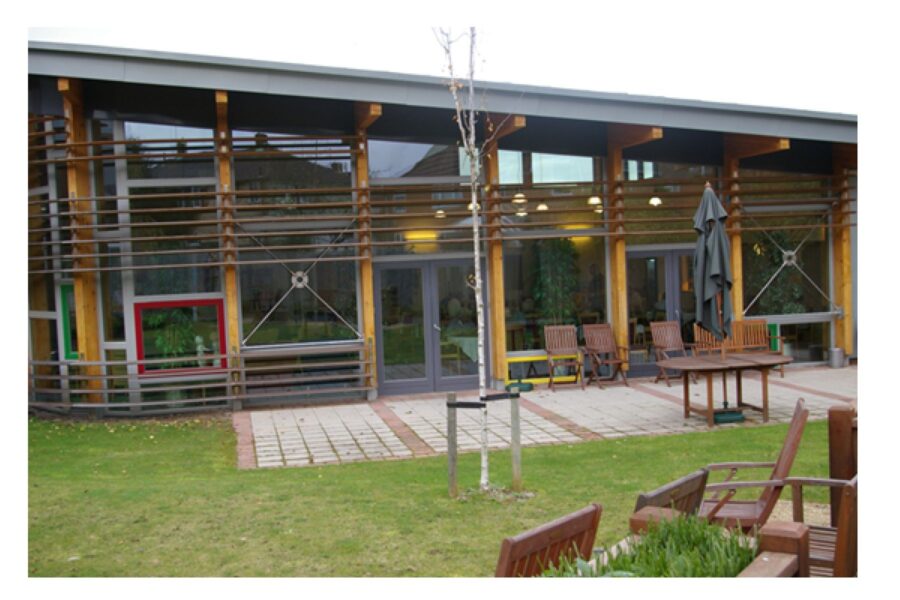
Rule 3: Make sure there is plenty of room for the heat recovery ventilation unit and ducting
Heat recovery ventilation is an essential part of Passivhaus design in cold and temperate climates. These systems, designed and installed correctly, recover much more heat than the amount of energy used to run them; ensure that ventilation is adequate, and indoor air quality is good, and prevent high levels of relative humidity that may promote mould growth.
At the early stages of a project, space should be allocated for the unit in the design close to an external wall where the intake and exhaust ducts can be routed. The ducts near the unit are quite large (>200mm diameter with their insulation) and space needs to be left above or adjacent to the unit, about equivalent in size to the unit itself. When insufficient space is left, duct routing and insulation are difficult to construct, the result often being poor ventilation and energy performance and noise caused by vibration.
The intake and exhaust ducts between the unit and the outside are full of cold air and, as such, are essentially an extension of the thermal envelope. Long ducts increase heat loss area, whilst poorly insulated ducts have the same effect as uninsulated thermal elements and create a condensation risk. The design needs to ensure that these ducts are as short as possible and that there is good access for the installer to insulate them to maximize the thermal efficiency of the heat recovery system. The images below show the difference between a system with plenty of space and well-insulated ducts (right) and a system which was not carefully planned (left).
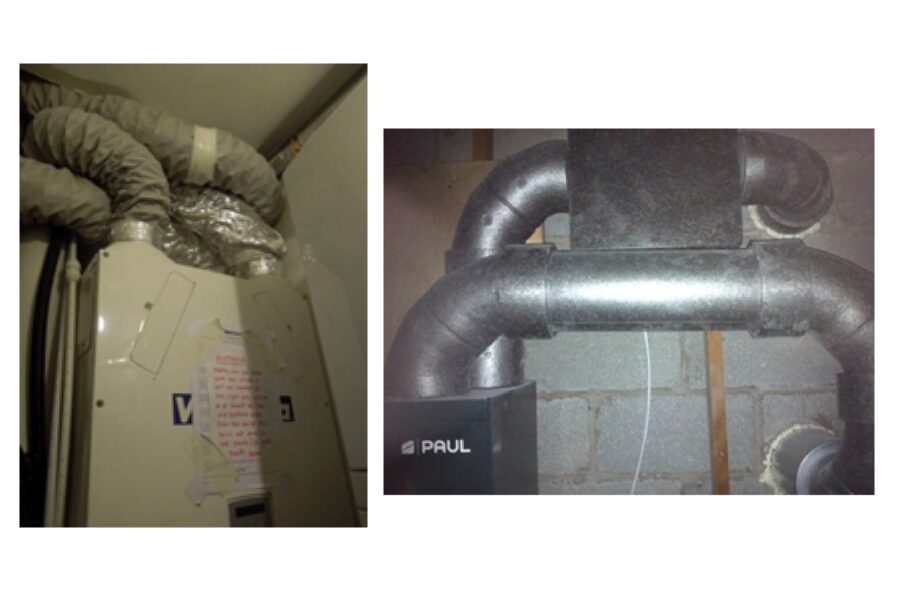
Consideration should also be given to how the ducting will be routed through the house, so that excessive boxing in is avoided. The image below shows well-planned duct routing.
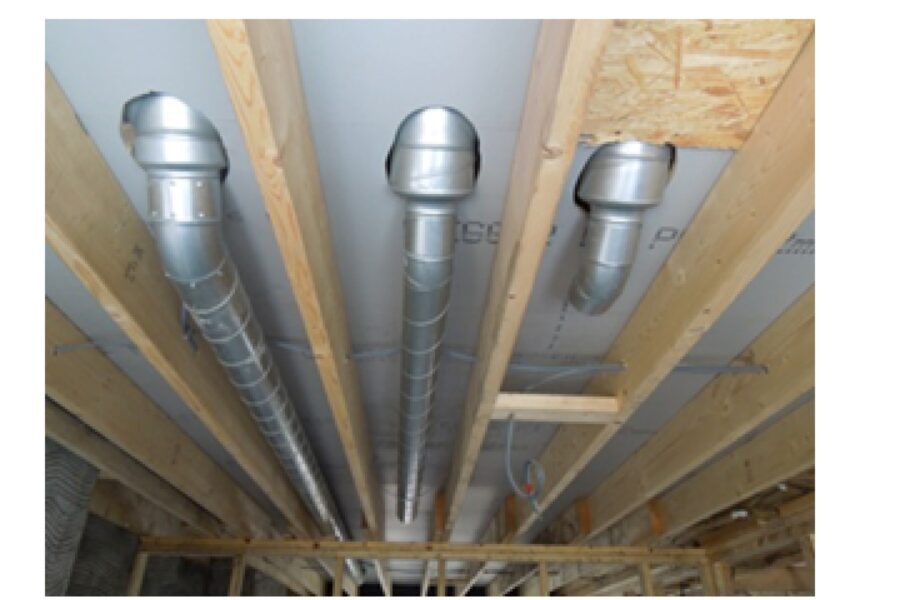
Passivhaus is based on building physics, so what applies in this article to Passivhaus buildings applies to any building where high energy performance is required. Whilst Passivhaus design can be complex and involved, following these simple rules at the outset makes the job of the design team and the builder much easier and increases the potential for achieving a very high-performance building or Passivhaus.
For further reading, we recommend the Passivhaus Trust’s excellent: ‘How to Build a Passivhaus: Passivhaus Rules of Thumb’